Autogenous Welding KTIG Video Demonstration WB ALLOYS
>> YOUR LINK HERE: ___ http://youtube.com/watch?v=3l480J13j1U
To arrange a demonstration contact • Glasgow: 0141 9404730 • Aberdeen: 01224 870052 • South England: 07852 986430 • North England: 07966 366270 • Material: Stainless Steel • Diameter: 10inch • Thickness: 10mm • Weld Time: 2m 31s • A revolution in welding technology • A relentless focus on welding's holy-grail; K-TIG welding systems perform welds up to 16mm in a single pass, while eliminating the need for filler wire, edge bevelling and skilled operators. K-TIG's value proposition is as powerful as it is straightforward. Productivity up, Costs down, Payback measured in months, not years • Produces flawless welds up to 100x faster than TIG welding in materials up to 16mm in thickness. • The result of ten years of research and four years of product trials in six countries has resulted in a new welding technology of extraordinary speed and simplicity. Welcome to K-TIG a fusion of technology, dedication and inspiration. • K-TIG is dedicated to the development of next-generation welding technologies. • Our team has unique expertise in advanced physics, materials science, weld engineering and plant automation. Our customer's aspirations are the central focus of both our research and product philosophy. Our people strive for nothing less than order-of magnitude productivity gains with every K-TIG product developed. • A welding process with extraordinary speed in thick materials, a 6 hour TIG weld completed in 3 minutes, K-TIG provides order-of-magnitude increases in productivity, with welding speeds up to 100x faster than conventional TIG/GTAW welding. • Nuclear grade weld quality comes standard. • Precision welding at its finest • A K-TIG weld is performed autogenously, without the need for filler wire, in a single full-penetration pass. The resulting weld is 100% parent material, without multiple fusion lines, virtually eliminating the potential for inclusions, porosity and other defects typical of many welding processes. K-TIG's ripple-free weld pool provides an exceptional quality cap and root that requires no back-gouging, finishing, cleaning or grinding. • The K-TIG welding system executes programmable weld sequences that adjust weld parameters dynamically to ensure exceptional • More materials. • Titanium • Zirconium • Stainless steels • Hastelloys • Niobium • Ferroniobium Alloys • Inconel • Incoloy • Nimonic • Cobalt alloys • Nickel alloys • Super alloys • Monel • Bisalloys • Carbon steels. • Incredible results on more materials. In a single pass K-TIG provides exceptional results across the widest range of exotic and conventional materials, and excels in medium to heavy gauge austenitic metals. • K-TIG welding is a low distortion process. Unlike plasma, laser and electron beam welding, K-TIG it is tolerant to imperfections and creates a highly stable, self-correcting full-penetration keyhole across a wide spectrum of specialist metals quality welds that are repeatable -- every time. • K-TIG's controllers are designed to integrate with virtually any form of plant automation equipment, from robots and seamers to rotators and positioners, and can control dozens of external devices. • If connected to the internet, K-TIG controllers update their firmware and software from K-TIG in the background, automatically. • Advanced welding for advanced manufacturing. • A high performance process for specialised industry applications, K-TIG has application across a wide range of industries where mission-critical quality, speed and cost-effectiveness are paramount, including: • Tube pipe manufacturing • Heat exchange • Oil Gas • Ship building • Defence Aerospace • Pressure, suction cryogenic vessels • Nuclear industries • Corrosion resistant vessels • Minerals processing • Production plants • Power generation • Filtration and water treatment • Reducing the footprint of fabrication, committed to reduced energy consumption. • Industrial fabrication, and the welding process in particular, is a highly energy intensive process involving the consumption of large quantities of gas, electricity and consumables. • K-TIG consumes as little as 1/20th of the energy and gas consumed by TIG/GTAW for the same weld, dramatically reducing the carbon footprint of our customers. • We're committed to the development of technologies which reduce energy consumption, improve the sustainability of our industry and improve occupational health and safety. • K-TIG's commitment to its fabrication customers is absolute. It is at the heart of everything that we do. • We think, live and breathe production welding. We take great pride in commissioning every K-TIG system, training our customer's teams and integrating K-TIG into production environments ranging from simple to highly complex. • The K-TIG welding process involves a specially controlled high current arc which opens a full-penetration keyhole in the join between the two surfaces to be welded. • http://www.wballoys.co.uk
#############################
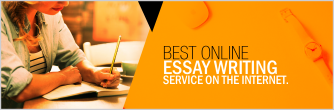