Making Springs Easy Inexpensive amp Safe
>> YOUR LINK HERE: ___ http://youtube.com/watch?v=lhQBz6qoTNc
How To Make Springs, Making Springs The Easy, Inexpensive, Safe Way. • • WARNING: I can't stress enough to always wear full eye protection (regular glasses are not good enough) any time dealing with spring wire or making springs, one mishap with it near the eyes and it's off the the hospital and possibly permanent vision damage. I know you know this, it's just my disclaimer to use the project in this video at your own risk. • • Ever needed a small coil spring but couldn’t find the right one or it was expensive? Well I’ve got just the thing for you. Check out this clip of my spring making jig and stay tuned for details on how to make your own custom springs! • This spring making jig a unique way to make quality custom springs easily, inexpensively, and safely. It doesn’t require a several thousand dollar metal lathe or other special equipment, the jig is easy to build, the spools of spring wire are not expensive, and for safety reasons design is completely hands-off the spring wire when the spring is being formed. • If any questions or other improvements for this spring maker jig please let me know. There is a Sketchup CAD model available for this design if you’d like to make this jig. • Please comment, like, share, subscribe to my channel. And if you have an idea for a future project you like to see just let me know. • Project Details: • This prototype is made from scrap ¾” thick wood, almost any type of wood could be used including plywood. First the jig clamps down to the workbench. There’s a hand crank with a bolt that screws threw T-nuts on the jig. This bolt is the mandrel that the spring wire wraps around to make the coil spring. The jig is setup for three different size bolts and the bolt used determines the coil spring diameter and the pitch of the spring winding. A ¼” bolt is installed right now and almost any size bolt can be added. • There are several sets of holes drilled in the jig to screw down metal alignment plates. These plates hold the spring wire in a fixed position and also apply a constant pull force as the coil spring is wound. The inside plate has a notch cut in it with a dremil tool that the spring wire passes through. • This is the process to make a coil spring... Start with a cut piece of wire. Feed the wire through the alignment plates. Adjust the mandrel bolt such that the notch cut in the bolt with a dremil tool is in-line with the notch in the alignment plates. Feed the wire into the notch on the bolt and hand tighten the nut to secure the spring wire to the bolt. Crank the handle clockwise until all wire is coiled around the bolt. Remove the nut off the bolt. Hold the spring and turn the crank handle counter clockwise until spring is able to slide off the bolt. • To make a tension spring, first clip or dremil off excess wire ends, use a screw drive to separate out one full loop at the end of the spring, using needle nose pliers put a 90degree bend on this end loop, then do same for other side of the spring. To make a compression skip the step of bending the end loops and pull apart the spring until it resting length is as desired. To make a torsion spring, leave the excess wire ends in place. It will be necessary to touch the wire ends with needle nose pliers to the desired shape. • The video shows the spring wire used and the supplier name, it was purchased off Amazon, I can recommend using this spring wire brand as it was inexpensive and has good spring properties. I purchased 0.051”, 0.037”, and 0.020” wire to use for large, medium, and small springs. • Wanted to mention working with spring wire can be dangerous so please always wear full eye protection whenever handling it. Also, if you decide to make this jig, do so at your own risk. This said, I believe this jig is the safest method to make springs yourself. • Regards to spring wire diameter selection, the ideal situation is that wire diameter equal to or less than the mandrel bolt pitch for example the ¼” bolt has a 20 pitch which is 0.050”, and so this close to perfect for 0.051” diameter wire I purchased. If the bolt pitch is greater than the wire diameter there will be an air gap between the windings. In some cases this would be desired such as compression spring. If wire diameter is greater than the bolt pitch, it wouldn’t wind properly. • Google Sketchup CAD tool was used for the upfront design the CAD model for this project is located on the Sketchup official model database at the below link in case it may be help with your project: https://3dwarehouse.sketchup.com/. • Type in 'Making Springs', or you could type in my user name Dumas5000 to find the CAD model. • Sketchup is a free CAD tool. • Search term on amazon for an example spring wire used with this video: High Carbon Steel Wire, #2B (Smooth) Finish, Full Hard Temper, ASTM A228 • If any questions or improvements for this project please comment below. And if you liked the video, please like subscribe to my channel for more.
#############################
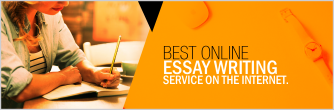