Concrete Crack Injection Polyurethane Water Stop Leak Sealing Systems Sealboss
>> YOUR LINK HERE: ___ http://youtube.com/watch?v=pb47qofi5c8
https://sealboss.com/leak-seal-inject... 714-662-4445 • How to Seal Leaking Concrete Cracks with PU Foam Injection • Zoo Exhibit Crack Repair Introduction • • The Gorilla Exhibit was closed for renovations and repairs. which included the sealing of concrete cracks that caused water intrusion, structural erosion and unsightly efflorescence and stains. • Concrete crack injection with polyurethane foam resin was the choice of repair to resolve water bearing crack leaks. Crack related damages were located at a walkway under a lofted area with multiple windows and decorative shotcrete structures where gorillas could sit and be viewed by people walking through the exhibit. • The cracks were covered in efflorescence could be seen on the walls below the lofted area as well as cracks coming off the cold joints around the precast window framing. • The crack dimensions ranged from hairline to 1/4″ joint seams with varying degrees of water intrusion and active leaks causing heavy efflorescence build up. The roof and lofted area collect and feed water during snow melt and heavy rains. • SealBoss provided an on-site technical representative to consult with the contractor on injection methods using NSF/ANSI 61 Drinking Water Contact Certified injection grout, a high-pressure injection pump and mechanical injection packers. • The Crack Injection Procedure Explained • Repair Method • Prior to injection, the contractor had to first prep the cracks by removing any efflorescence and dirt build-up from the face of the crack using a wire brush. • Once the cracks were visible an injection plan was established to address the leaks working from the low point up. • Using the SealBoss high pressure injection system — hydro-active, hydrophobic polyurethane foam resin, injection packers and polyurethane crack injection pump — hydro-active foam resin is injected into the cracks, expanding on contact with moisture and displacing any water in the process while creating an airtight watertight seal. • Crack Injection Details • The Standard Injection Procedure • One side of the lofted area had three significant cracks that resulted in substantial active leaks. The east wall presented larger actively leaking cracks. Further, cracks and cold joints from a precast window frame created an area of leakage that needed to be injected. • In those areas, SealBoss 1/2 inch injection packers were placed according to SealBoss Standard Recommendations, roughly 4” from the crack in ½” holes that were drilled at a 45-degree angle back into the crack. SealBoss 1510 Water Stop Foam was injected until positive refusal of the hydro-active resin was visible from the face of the crack as well as on the exterior side of the wall when a through crack was injected. • Starting with the lowest point of the cracks, SealBoss 1510 Leak Sealing Foam Grout was injected until positive refusal was observed on the interior and exterior of the wall. Due to the temperature of the wall, around 36 degrees Fahrenheit, the contractor was advised to use a condition the resin to room temperature prior to use as well as adding 15% of SealBoss 1510 Accelerator/Catalyst to compensate for the cooler ambient and substrate temperature — cold temperatures slow down the chemical reaction of the injection grout. • The Complex Injection Procedure • The west wall had a complex crack system. Multiple cracks had developed connecting to a larger initial crack, creating a spider-web crack pattern. Due to the complexity of the crack system and intersections of cracks, the injection procedure was modified from the standard alternating “zipper” pattern typically recommended. Cracks were so close in proximity that packers needed to be strategically ‘custom’ placed to increase the chance for each packer drill hole to successfully intersect with the crack. • Starting at the low point of crack, the Water Stop Foam was injected till and foam travel was observerd at a distance from the point of injection intersecting into other cracks. This meant that multiple cracks could be addressed from one point of injection without the need for drilling too many injection port holes. • As the resin visibly moved up and out of the face of the crack, injection of that specific crack would be stopped so the resin could react and fully expand creating a seal. • Shortly thereafter, a secondary injection of the same packer was performed to penetrate even deeper into the crack and allow for further continuation of visible vertical foam resin travel.
#############################
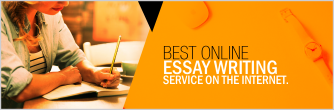