Claus Plant Fundamentals
#############################
Video Source: www.youtube.com/watch?v=bc7CA35JJlk
This is the second video in a mini series that provides an overview of the sulfur recovery process, covering: elemental sulfur, sulfur recovery industry, Claus plant fundamentals, SRU process units/equipment, and SRU intrumentation. • • Most sulfur plants are based on the Claus Process developed by Carl Freidrich Claus in 1883. He discovered that H2S reacted with air over a catalyst directly to form sulfur and water. The Claus process is a highly exothermic reaction with low efficiencies. Reaction control is difficult, and there is high risk of overheating the reactor. • • The modified Claus process includes a highly exothermic thermal combustion reaction section, followed by a moderately exothermic catalyst reactor section. • There are various different configurations, which are a function of the Acid Gas Feed Compositions, the Minimum Recovery Efficiency, the Maximum Throughput, and the available Utilities. • • This slide is to show that with the Claus process there is just that one reaction, where the furnace and converter are in one vessel. The modified-Claus, which is used in SRUs, has the reaction furnace and at least 2 downstream catalytic stages. • • Sulfur Handling: Stock piling at plant for future re-melt? Liquid, Prilling, Granules, or Slating for transport? • • For the highest recovery efficiencies, note that the Claus reaction is favored with decreasing temperature. Recovery efficiency is the amount of H2S that is converted to sulfur vapor and subsequently recovered in the condensers as a liquid. • Potential losses to Recovery Efficiency are: • Catalyst Deactivation • Off-Ratio Control (Tail Gas Analyzer) • Excessive Converter Dewpoint Margins • Poor COS, CS2 Hydrolysis • Poor Demister Pad Operation/Sulfur Fog • High Final Condenser Outlet Temperature • Excessive Turndown • Day-to-Day Operational Upsets • Depending on the amount of H2S in the feed stream, a split-flow process may be preferred over a straight-through one. When the H2S concentration is less than 50%, a split-flow reaction furnace setup is desired, where 1/3 of the acid gas is burned in the furnace, and the other 2/3rds bypasses it. The 1/3 will be completely oxidized in the furnace so that a 2:1 H2S to SO2 ratio is still achieved in the downstream converter. • We want to ensure each catalytic stage has an H2S to SO2 ratio of 2:1, to do this the Ratio controller controls the main combustion air flow based on the acid gas flow rate. For finer tuning, the tail gas analyzer calculates the Air Demand Signal, or ADA, which regulates the trim air flow to the furnace. • The key takeaway from this graph is that anytime the air demand signal goes outside of +/- 0.5 percent, there will be an immediate loss in recovery efficiency. Another takeaway is that the loss in recovery is worse when the air demand goes negative, this occurs when the ratio gets too high. • Thanks for watching! For more videos on sulfur recovery, subscribe to our page. Also visit our website http://sulfurrecovery.com/, and sign up for our monthly newsletter here: http://sulfurrecovery.com/Newsletter/
#############################
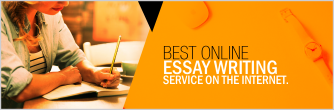