Fine wire wedge bonding
>> YOUR LINK HERE: ___ http://youtube.com/watch?v=GhdoN8t23rY
To find out more about TWI's technologies please visit https://www.twi-global.com/who-we-are... or to read more about TWI's training courses visit http://www.twitraining.com/ • TWI has been actively involved in the development and testing of electronic devices and sensors for over 40 years, helping Members to produce cost-effective, reliable products and solutions by providing authoritative advice and guidance on materials and process selection, prototyping and production line troubleshooting. • Electronics, photonics and sensors are fundamental to the operation of most of today's products and infrastructure, and can consequently have a significant influence on a company's success. TWI offers support on the full range of applications. • WEDGE BONDING is a method of welding usually small wires for making electrical contact between electronic components. It is an ultrasonic process, so it is a solid state weld with very localised low heat input. A wedge tool (think rounded end chisel) presses a wire against the surface the wire is to be bonded to. Ultrasonic vibration is applied which scrubs the wire onto the surface and removes oxides to encourage bonding. A load is applied to the tool which forges the wire onto the surface to produce the weld, typically reducing the wire thickness by 50%. The process can be done cold for aluminium wires, or with a small background heating for example with gold wires. • Wire diameters vary from ~ 10 microns to ~1mm. In practice this is done by automatic machines which feed the wire through a hole in the tool, which has a secondary edge that can cut the wire to leave a wire-bond stitch connection, with a weld at each end. These machines can do up to 8 wire-bonds per second. • Wedge bonded wire-bonds (ie with a wedge bond at each end) are very fast and low cost, and ideal for where many parallel wires are required, such as micro-processors. • For applications with many variations in the wire bond direction then a sister process called BALL-BONDING is used where for the first joint the wire is melted back to form a small ball which is ultrasonically bonded, and allows the wire to be pulled through the tool in any direction before the other stitch end is bonded and cut. • Applications include nearly all volume semiconductor assemblies - including microprocessors (1000's of bonds per device), power devices (thicker wires), and RF and Microwave components for eg mobile communications (flat ribbon shaped wires are done with this process). So this process is essential to every piece of electronic or electrically controlled equipment in every market sector. So, numerically by number of welds produced, wedge and ball bonding are the world's most widely used welding processes.
#############################
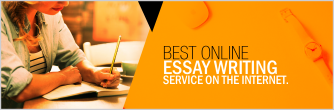
New on site